เทคโนโลยีการฉีดขึ้นรูปสำหรับชิ้นส่วนพลาสติกที่มีความแข็งแรงสูง
การเข้าใจเทคโนโลยีการเจาะ
การเจาะเป็นกระบวนการผลิตที่สําคัญที่จําเป็นในการผลิตชิ้นส่วนโดยการเจาะวัสดุหลอมลงในหม้อ การ ทํา งาน ที่ ดี ที่ สุด เนื่องจากความสามารถหลากหลายของมัน การเจาะเป็นเป็นสิ่งจําเป็นในอุตสาหกรรมต่างๆ รวมถึงการผลิตรถยนต์ สินค้าผู้บริโภค และอิเล็กทรอนิกส์
การพัฒนาของการเจาะย่อย้อนกลับไปสู่ศตวรรษที่ 19 ในยุคนี้ มีจุดสําคัญคือเครื่องปัดฉีดพลาสติกครั้งแรก ที่จอห์น เวสลีย์ ไฮแอทต์ ได้รับสิทธิ์ฉีดฉีดในปี 1872 การ สร้าง ของ ไฮ แทท ทํา ให้ มี การ ตัด แบบ หม้อ หม้อ หม้อ ใน สมัย นี้ โดย นํา มา ใช้ วิธี การ ที่ เปลี่ยนแปลง ไป ใน การ สร้าง ส่วน หม้อ หม้อ หม้อ หม้อ แม้ ว่า วิธี การ นี้ จะ ง่าย กว่า เทคโนโลยี ใน ปัจจ
กระบวนการเจาะหมักมีหลายขั้นตอนสําคัญ เริ่มต้น วัสดุ, ปกติเป็นพลาสติก, จะละลายในอุณหภูมิสูง. จากนั้นมันจะถูกฉีดเข้าไปในช่องของหมัก ภายใต้ความดันสูง เมื่อเข้าสู่ภายใน วัสดุจะเย็นและแข็งขึ้น ปลายเป็นการเปิดเปลือก วงจรนี้ซ้ําขึ้นเพื่อผลิตองค์ประกอบที่สอดคล้องและแม่นยํา โดยมีตัวช่วยทางสายตาที่อาจช่วยให้เข้าใจขั้นตอนรายละเอียดที่เกี่ยวข้องมากขึ้น
ประโยชน์ สําคัญ ของ การ ตัด หม้อ ด้วย การ หมัด
การเจาะหมักมีชื่อเสียงสําหรับการประหยัดประสิทธิภาพของมัน โดยเฉพาะอย่างยิ่งในกรณีการผลิตขนาดใหญ่ กระบวนการนี้ลดค่าใช้จ่ายรวมในการผลิตชิ้นส่วนพลาสติกลงอย่างมาก เมื่อเทียบกับวิธีอื่น การศึกษาหนึ่งชี้ให้เห็นว่า การเจาะแบบยาง ค่าใช้จ่ายต่อหน่วยลดลงอย่างมาก เมื่อปริมาณเพิ่มขึ้น ทําให้มันเหมาะสําหรับการผลิตปริมาณสูง การประหยัดนี้กลายเป็นที่ชัดเจนเมื่อพิจารณาค่าใช้จ่าย เช่นแรงงานและสิ่งของที่เสีย ซึ่งถูกลดลงอย่างน้อยผ่านธรรมชาติที่ประสิทธิภาพของการเจาะ
นอกจากนี้ การเจาะหมักยังมีประสิทธิภาพการผลิตสูง โดยมีเวลารอบที่เร็ว ตัวอย่างเช่น เวลารอบในการเจาะสามารถระยะยาวจากไม่กี่วินาทีถึงนาที ขึ้นอยู่กับความซับซ้อนและขนาดของชิ้นส่วน ประสิทธิภาพนี้แปลว่าความสามารถในการผลิตชิ้นส่วนเป็นล้านๆ อย่างต่อเนื่องและรวดเร็ว ซึ่งเป็นประโยชน์ในอุตสาหกรรมที่เวลาในการตลาดเป็นสิ่งสําคัญ
ความหลากหลายของการเจาะหมักในแง่ของการออกแบบและวัสดุเป็นข้อดีที่สําคัญอีกอย่าง กระบวนการนี้รองรับพลาสติกและพอลิมเมอร์หลายชนิด ทําให้ผู้ผลิตสามารถสร้างการออกแบบที่ซับซ้อนและรูปร่างที่ซับซ้อน ซึ่งจะมีความท้าทายในการบรรลุด้วยวิธีการผลิตอื่น ๆ ความสามารถในการปรับแต่งชิ้นส่วนเพื่อตอบสนองความต้องการการออกแบบที่เฉพาะเจาะจง เป็นสิ่งสําคัญในอุตสาหกรรม เช่น ออโต้และอิเล็กทรอนิกส์ผู้บริโภค ที่ทั้งความสวยงามและความเป็นไปได้มีความสําคัญ โดยให้ตัวเลือกสําหรับวัสดุต่างๆ และกณิตศาสตร์ที่ซับซ้อน การเจาะหมักให้ผู้ผลิตความยืดหยุ่นที่จําเป็นต้องตอบสนองความต้องการของอุตสาหกรรมที่หลากหลาย
การใช้งานในอุตสาหกรรมของการพิมพ์ฉีด
การเจาะหมักถูกใช้อย่างมากในหลายอุตสาหกรรมหลัก แสดงถึงความสามารถและประสิทธิภาพของมัน ตัวอย่างเช่น อุตสาหกรรมรถยนต์ ใช้วิธีนี้มากในการผลิตส่วนประกอบ เช่น ดัสบอร์ดและถังน้ํามัน ตามข้อมูลของอุตสาหกรรม ประมาณ 30% ของอะไหล่รถยนต์ถูกผลิตโดยใช้การเจาะยาง ส่งผลให้มีรถยนต์ที่เบาและประหยัดน้ํามันมากขึ้น
ในสาขาการแพทย์ การเจาะเป็นเครื่องยนต์ เป็นสิ่งสําคัญในการผลิตฉีดยา, ถังยา และอุปกรณ์การแพทย์ที่ซับซ้อน ผลิตภัณฑ์เหล่านี้ต้องปฏิบัติตามมาตรฐานการกํากับที่เข้มงวด เพื่อให้มั่นใจในความปลอดภัยและความน่าเชื่อถือในสภาพแวดล้อมการดูแลสุขภาพ ความสามารถในการผลิตชิ้นส่วนที่แม่นยําและสะอาดไว เป็นสิ่งสําคัญ และการเจาะเป็นเป็นหนึ่งในกระบวนการไม่กี่อย่างที่สามารถตอบสนองความต้องการที่เข้มงวดเหล่านี้ได้อย่างมีประสิทธิภาพ
นอกจากนี้ สินค้าผู้บริโภคตั้งแต่วัสดุครัวเรือนถึงกล่องของอิเล็กทรอนิกส์มักจะเป็นผลจากการพิมพ์ฉีด เนื่องจากความสามารถในการผลิตปริมาณมากในราคาต่ํา สินค้าประจําวัน เช่น แปรงสีฟัน และเปลือกมือถือมักถูกสร้างขึ้นโดยใช้วิธีนี้ โดยเน้นการใช้งานและผลกระทบที่เกิดขึ้นในชีวิตประจําวัน
อุตสาหกรรมเครื่องบินและอวกาศยังได้รับประโยชน์จากการเจาะแบบ โดยผลิตส่วนประกอบเบา ๆ แต่ทนทาน เช่น แผ่นและกระเป๋าเรือน ที่เพิ่มผลงานของเครื่องบินและประหยัดน้ํามัน องค์ประกอบเหล่านี้ตอบสนองความต้องการที่เข้มงวดสําหรับความแข็งแรงและความทนความร้อนที่จําเป็นสําหรับสภาพความสูงสูง
ปัญหา และ ข้อ จํากัด ของ การ ตัด หม้อ ด้วย การ สูบ
การเจาะยางต้องใช้เงินลงทุนครั้งแรกอย่างมาก โดยเฉพาะในเครื่องจักรและหม้อ ค่า ของ โมล์ม ที่ มี ช่อง เดียว ง่าย ๆ อาจ สูง ถึง 2,000 ดอลลาร์ ส่วน โมล์ม ที่ มี หลายช่อง ที่ ซับซ้อน อาจ สูง กว่า 100,000 ดอลลาร์ ค่าใช้จ่ายต้นทุนสูงนี้ ทําให้มันไม่เหมาะสําหรับการผลิตในปริมาณน้อย การจัดงบประมาณและการวิเคราะห์ค่าใช้จ่ายที่แม่นยําเป็นสิ่งสําคัญสําหรับผู้ผลิต เพื่อกําหนดความเป็นไปได้ของการเจาะหมักสําหรับโครงการของพวกเขา
ขยะวัสดุและผลกระทบต่อสิ่งแวดล้อมเป็นปัญหาสําคัญในการเจาะ แม้ว่าระบบวงจรปิดที่ออกแบบมาเพื่อลดขยะให้น้อยที่สุด แต่วัสดุพลาสติกที่ใช้ในการผลิตยังคงส่งผลให้มีขยะพลาสติกทั้งหมด รายงาน พลาสติกส์ ยูโรป์ บอก ว่า การ ผลิต พลาสติก ทั่ว โลก ได้ เพิ่ม เป็น หลาย แสน ล้าน ตัน ใน ปี แต่ มี เพียง ส่วน น้อย เท่า นั้น ที่ ถูก ทํา ใหม่ การสมดุลประสิทธิภาพของวัสดุกับความรับผิดชอบต่อสิ่งแวดล้อม ยังคงเป็นโจทย์ยากต่ออุตสาหกรรม
ความท้าทายอีกอย่างในการเจาะเป็นปัญหาของเวลานําและความยืดหยุ่น เมื่อมีหม้อสร้างแล้ว การเปลี่ยนแปลงตารางการผลิต หรือการออกแบบอาจยากและใช้เวลา การผลิตหม้ออาจใช้เวลา 5 ถึง 10 สัปดาห์ ทําให้มันท้าทายในการปรับตัวกับการเปลี่ยนแปลงตลาดที่ทันใดหรือการปรับปรุงการออกแบบ ความแข็งแรงนี้มักจะต้องการการวางแผนและการลงทุนล่วงหน้าอย่างรอบคอบ เพื่อให้แน่ใจว่าการสอดคล้องกับเป้าหมายการผลิต
สินค้าการพิมพ์ฉีดที่นิยม
การเจาะหมักทําให้สามารถผลิตส่วนประกอบที่สําคัญหลากหลายสําหรับการใช้งานที่แตกต่างกัน สินค้าที่น่าสนใจคือ สตั๊กยางพลาสติกอ่อน TPE ออกแบบมาเป็นพิเศษสําหรับปุ่มรถ ส่วนประกอบนี้ถูกออกแบบมาเพื่อตอบสนองความต้องการที่เข้มงวด ทั้งสําหรับเส้น径ภายนอกและความแข็งแรง, การรับประกันคุณภาพที่คงที่และความน่าเชื่อถือในแอปพลิเคชั่นรถยนต์.
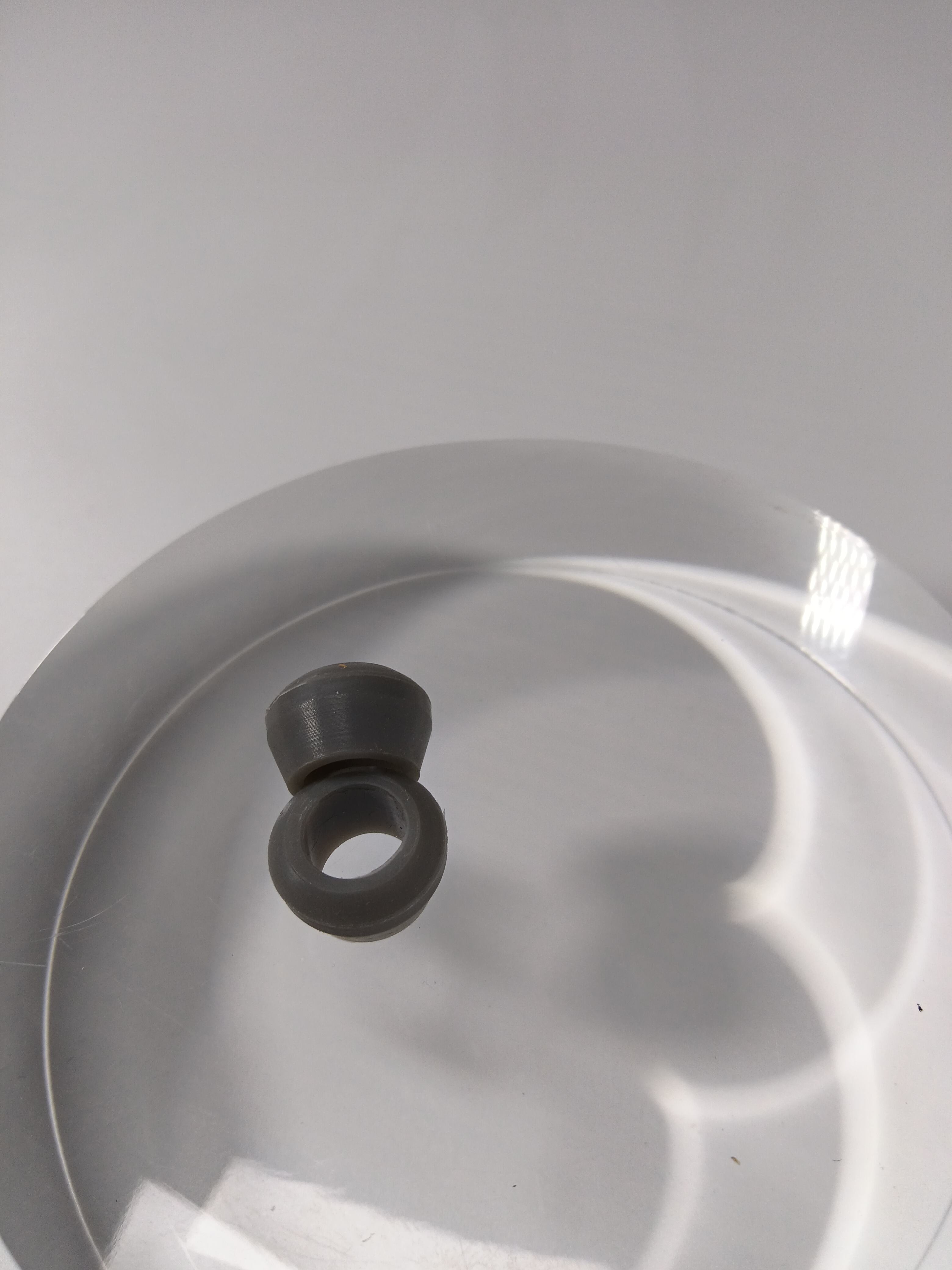
สินค้าสําคัญอีกอย่างคือ หมวกระตุ้นอาการเตือนอัลลูมิเนียม 6061 - ไม่ สินค้านี้นําสิทธิประโยชน์จาก คุณสมบัติที่ดีเยี่ยมของอลูมิเนียม 6061 ทําให้มันเป็นตัวเลือกที่ดีสําหรับการใช้งานด้านความปลอดภัย หมุนมีความแข็งแรงและทนทานสูง ทําให้เหมาะสําหรับการใช้ในระบบเตือนการค้าและบ้าน
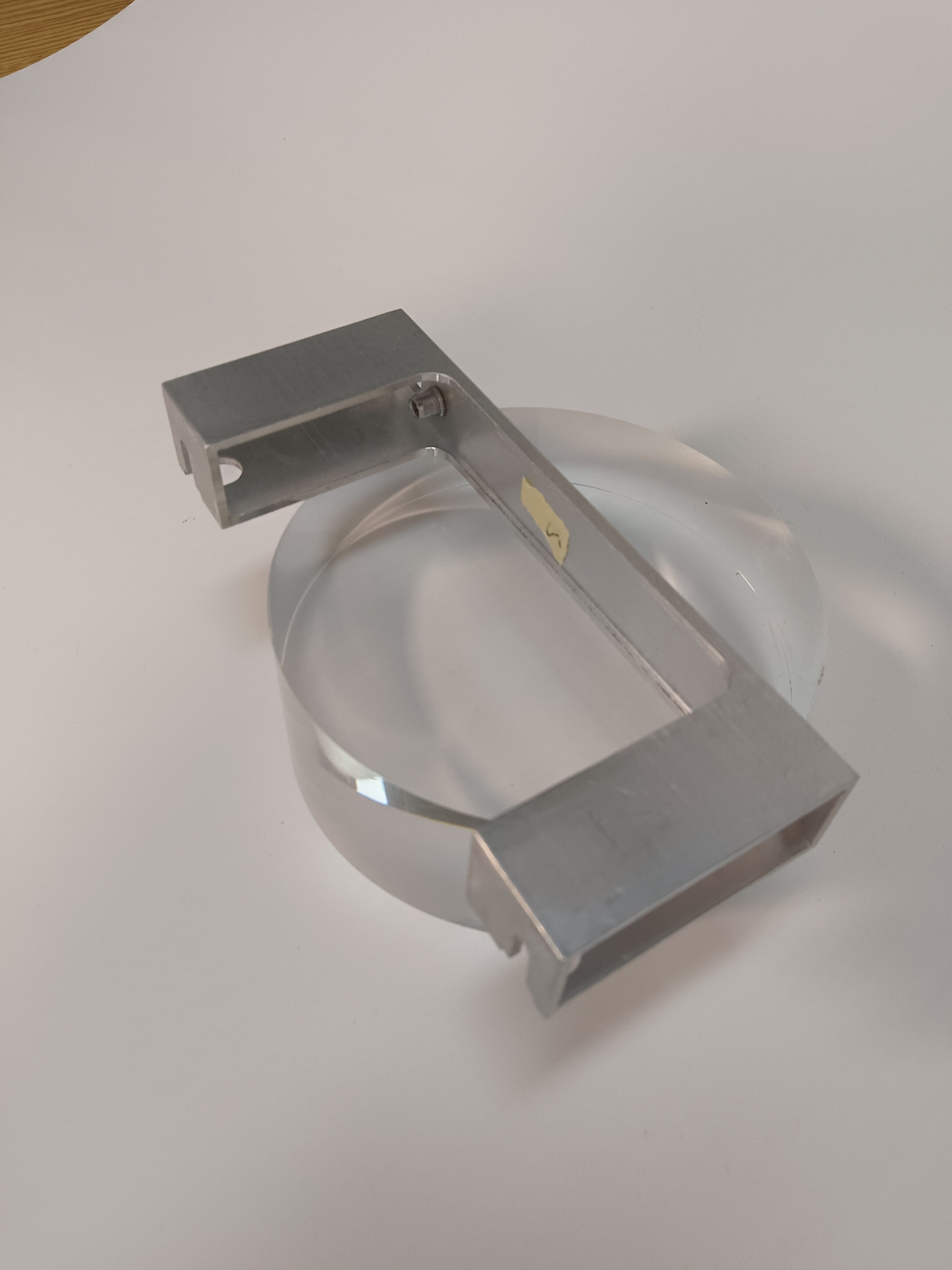
นอกจากนี้ ผู้ถือพัสดุพลาสติก PC ที่โปร่งใส เป็นสินค้าที่น่าสนใจ ที่มีความเห็นและความแข็งแรงอย่างพิเศษ ส่วนประกอบนี้มีประโยชน์อย่างยิ่งในแอพลิเคชั่นที่ต้องการการสังเกตเห็นชัดเจนของตัวถือพรานท์ เช่น ในอุปกรณ์มอเตอร์ และถูกออกแบบให้ผ่านการควบคุมคุณภาพอย่างเข้มงวดเพื่อให้มั่นใจ
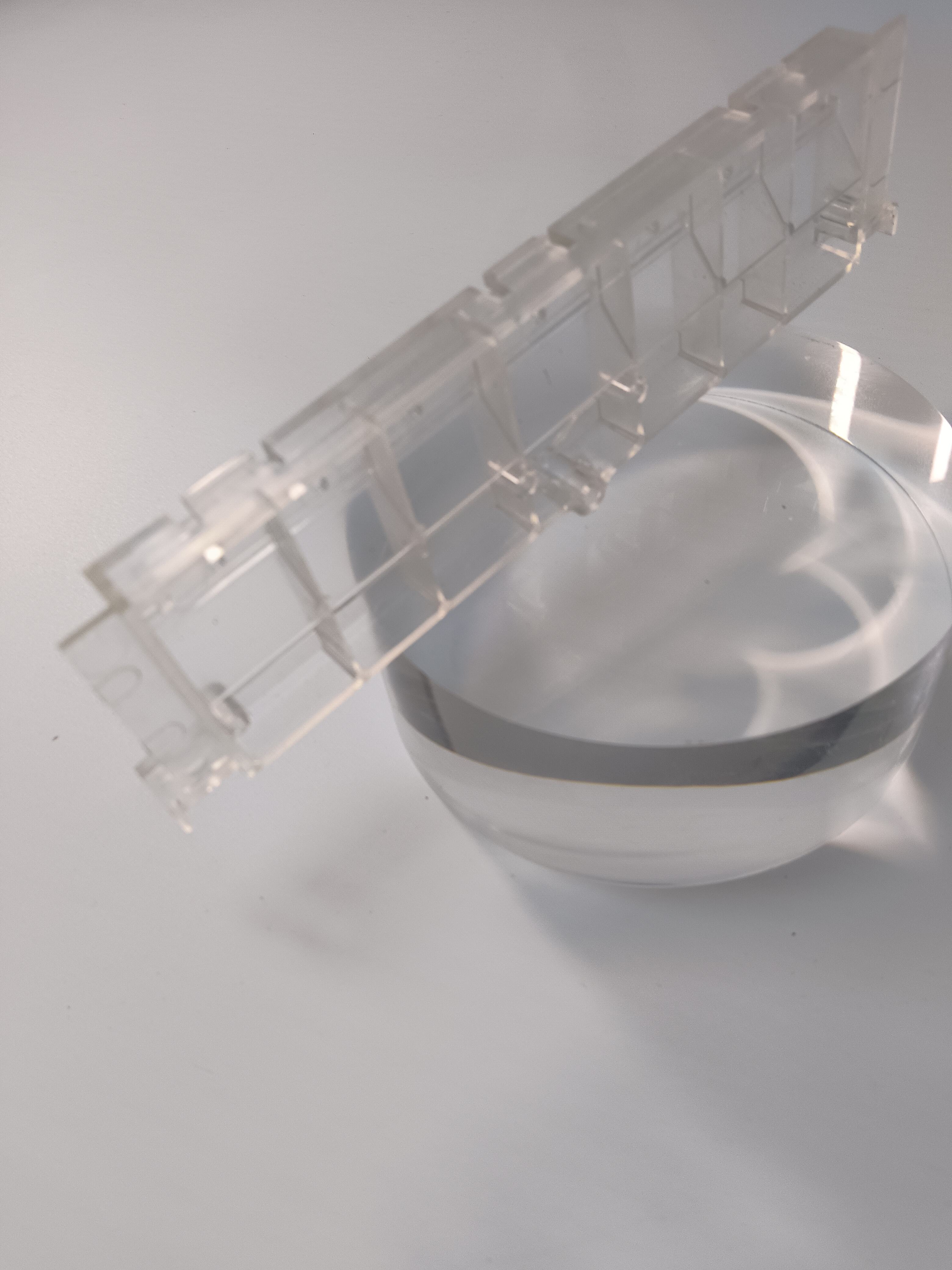
ผลิตภัณฑ์เหล่านี้เป็นตัวอย่างของการใช้งานและประโยชน์ที่หลากหลายของการเจาะเจาะในการผลิตส่วนประกอบเฉพาะสําหรับอุตสาหกรรมต่างๆ
แนวโน้ม ใน อนาคต ใน การ ตัด หม้อ หม้อ
อนาคตของการเจาะหมักถูกสร้างขึ้นโดยความก้าวหน้าที่สําคัญในวัสดุ เทคโนโลยี และวิธีการยั่งยืน หนึ่งในความพัฒนาที่น่าหวังที่สุด คือการเพิ่มพูนของพลาสติกจากชีวภาพ การวิจัยล่าสุดเน้นถึงศักยภาพในการลดผลกระทบต่อสิ่งแวดล้อมอย่างสําคัญ โดยยังคงคุณสมบัติที่จําเป็นสําหรับการใช้งานที่มีประสิทธิภาพสูง วัสดุจากชีวภาพสามารถเปลี่ยนอุตสาหกรรมโดยการนําเสนอทางเลือกที่ยั่งยืนกับพลาสติกพื้นฐานน้ํามันแบบดั้งเดิม โดยไม่เสียสละคุณภาพหรือความน่าเชื่อถือ
การ นวัตกรรม ทาง เทคโนโลยี ยัง ทํา ให้ กระบวนการ ตัด หม้อ ด้วย การ หมัด หม้อ ด้วย การ หมัด หม้อ ด้วย การ หมัด หม้อ ด้วย การ หมัด หมัด หม้อ ด้วย การบูรณาการเทคโนโลยีพิมพ์ 3 มิติกับการพิมพ์ฉีดแบบดั้งเดิม เป็นแนวโน้มที่น่าสังเกต แนวทางแบบไฮบริดนี้ทําให้สามารถสร้างต้นแบบและปรับแต่งแบบได้อย่างรวดเร็ว ก่อนการผลิตจํานวนมาก โดยเพิ่มประสิทธิภาพและลดเวลาในการนําเสนอ บริษัทชั้นนําอย่าง Stratasys และ DDM ได้เริ่มนําเทคโนโลยีเหล่านี้มาใช้แล้ว ทําให้มีการเปิดช่องทางสู่ยุคใหม่ของการผลิตแบบยืดหยุ่น นอกจากนี้ การพัฒนาในด้านอัตโนมัติ ได้ทําให้การผลิตดีขึ้น ลดความผิดพลาดและลดต้นทุน
ความยั่งยืนเป็นพื้นที่สําคัญในการเน้นในอุตสาหกรรมการเจาะ บริษัทกําลังนํามาใช้ในจํานวนมากในเรื่องการรีไซเคิล ซึ่งช่วยลดการทิ้งและประหยัดทรัพยากร นอกจากนี้ กระบวนการที่ประหยัดพลังงานก็กลายเป็นแนวปฏิบัติทั่วไป โดยผลักดันโดยความมุ่งมั่นของอุตสาหกรรมในการลดการก่อสร้างคาร์บอน ตามที่เน้นในแนวโน้มของอุตสาหกรรมล่าสุด แนวทางเหล่านี้ไม่เพียงแค่สนับสนุนเป้าหมายสิ่งแวดล้อม แต่ยังเพิ่มประสิทธิภาพการดําเนินงานและประสิทธิภาพในเรื่องค่าใช้จ่าย ทําให้ผู้ผลิตสามารถตอบสนองความต้องการตลาดที่เพิ่มขึ้นอย่างยั่งยืน
สรุป: อนาคตของการพิมพ์ฉีด
สรุปคือ การเจาะยังคงเป็นรากฐานสําคัญในด้านการผลิต โดยมีลักษณะของประสิทธิภาพและความสามารถในการปรับปรุง คุณสมบัติเหล่านี้ย้ําบทบาทสําคัญในการสร้างความก้าวหน้าในอนาคตในกระบวนการผลิต ในขณะที่อุตสาหกรรมยังคงพัฒนา พลังงานสําหรับการเติบโตและนวัตกรรมในการพิมพ์ฉีดเป็นสําคัญ สัญญาต่อการต่อเนื่องผลต่อต้านด้านต่างๆ