Sprøytestøpingsteknologi for høystyrke plastdeler
Forståelse av injeksjonsformings teknologi
Injeksjonsforming er en avgjørende produksjonsprosess som er essensiell for å lage deler ved å spre smeltet materiale inn i en form. Understrykt for sin effektivitet, lar denne teknikken tilbake fast og nøyaktig masseproduksjon av komponenter, fra komplekse til enkle design. Grunnet sin versatilitet, er injeksjonsforming uerstattelig i ulike industrier, inkludert bilindustrien, forbrukergoder og elektronikk.
Utviklingen av injeksjonsforming strekker seg tilbake til det 19. århundre. I denne tidsperioden var et betydelig mileplass den første plastinjeksjonsformingsmaskinen, patentert av John Wesley Hyatt i 1872. Hyatts oppfinning banet veien for moderne injeksjonsforming ved å introdusere en revolusjonær metode for å lage formede deler, selv om den var enklere i forhold til dagens teknologi.
Injeksjonsformingsprosessen involverer flere nøkkeltrinn. Initiativt smeltes materialet, vanligvis plast, på høy temperatur. Deretter injiseres det inn i formhulen under høy trykk. Når det er inne, kjøles materialet av og fastner, og danner den ønskede delens form. Til slutt åpnes formen for å utskytte ferdigproduktet. Denne syklusen gjentas for å produsere konsekvente og nøyaktige komponenter, med potensielle visuelle hjelpemidler som forsterker forståelsen av de detaljerte trinnene som er inntatt.
Nøkkel fordeler ved injeksjonsforming
Injeksjonsforming er kjent for sin kostnadsfordel, særlig i storeproduksjons-scenarier. Denne prosessen senker dramatisk den totale produksjonskostnad av plastdeler i forhold til andre metoder. En studie understryket at med injeksjonsforming minker enhetskostnadene betydelig når volumet øker, noe som gjør det ideelt for høyvolumsproduksjon. Denne økonomiseringen blir synlig når man tar hensyn til kostnader som arbeidskraft og materialeavfall, som minimeres gjennom effektiviteten til injeksjonsforming.
Dessuten kjenner injeksjonsforming seg ved høy produksjons-effektivitet, merket av raske syltetider som tillater rask produksjon av deler. For eksempel kan syltetidene i injeksjonsforming variere fra noen sekunder til minutter, avhengig av kompleksiteten og størrelsen på delen. Denne effektiviteten oversetter seg til evnen til å produsere millioner av deler konsekvent og raskt, noe som er fordelsmessig i bransjer der markedsføringstiden er avgjørende.
Fleksibiliteten ved injeksjonsformning med hensyn til design og materialer er en annen viktig fordel. Denne prosessen støtter en bred vifte av plastikker og polymerer, noe som lar produsenter lage intrikate design og komplekse former som ville vært utfordrende å oppnå med andre produksjonsmetoder. Evnen til å tilpasse deler for å møte spesifikke designtilpasninger er avgjørende i industrier som bilindustrien og forbrukerelektronikk, hvor både estetikk og funksjonalitet er viktige. Ved å tilby valg av ulike materialer og komplekse geometrier gir injeksjonsformning produsenter den fleksibiliteten de trenger for å møte diverse industrikrav.
Bransjeapplikasjoner av injeksjonsformning
Injeksjonsforming brukes omfattende i flere store industrier, noe som viser dets fleksibilitet og effektivitet. Bilsjangeren avhenger sterkt av denne metoden for å produsere komponenter som instrumentbord og brannekammer. Ifølge bransjenyttigheter lager man omtrent 30% av bilenes deler ved hjelp av injeksjonsforming, noe som bidrar til lettere og mer bråndeffektive kjøretøy.
I helsevesenet er injeksjonsforming avgjørende for å lage sprut, flaske og komplekse medisinske apparater. Disse produktene må oppfylle strikte reguleringer for å sikre trygghet og pålitelighet i helsefagslige miljøer. Evnen til å produsere nøyaktige og sanitære komponenter raskt er avgjørende, og injeksjonsforming er en av de få prosessene som kan møte disse strenge kravene effektivt.
Dessuten omfatter forbrukervarene alt fra husholdningsartikler til elektronikkgehuser, som ofte er resultatet av injeksjonsmolding på grunn av dets evne til å produsere store volum til lav kostnad. Daglige produkter som tannbørster og mobiltelefongehuser lages vanligvis ved hjelp av denne metoden, noe som understreker dens brede bruk og innvirkning på dagliglivet.
Luftfartindustrien nyter også fordeler med injeksjonsmolding ved å fremstille lettvektige, likevel bestandige komponenter, såsom paneler og gehuser, som forbedrer flyets ytelse og bråndeffektivitet. Disse komponentene møter de strengt definerte kravene for styrke og varmebestandighet nødvendig for høyhetsforhold, noe som representerer en annen kritisk anvendelse av injeksjonsmoldingsteknologien.
Ufordelene og begrensninger ved injeksjonsmolding
Sprutforming krever en betydelig initialinvestering, særlig i maskineri og former. Kostnaden for en enkel enkelt-hulleform kan nå opp til 2 000 dollar, mens en kompleks flerhullerform kan overskride 100 000 dollar. Den høye oppstartskostnaden gjør det mindre realistisk for lave produksjonskjøringer. Nøyaktig budsjettsetting og kostnadsanalyse er avgjørende for produsenter for å vurdere hvorvidt sprutforming er veientatt for deres prosjekter.
Materialeavfall og miljøpåvirkning er betydelige bekymringer i sprutforming. Trods lukkede systemer som er utformet for å minimere avfall, bidrar plastmaterialer brukt i prosessen fortsatt til totalt plastavfall. Ifølge PlasticsEurope har den globale produksjonen av plast nådd hundrevis av millioner tons årlig, med bare en brøkdel som blir gjenbrukt. Å balansere materialeffektivitet med miljøansvarlig praksis forblir et utfordring for bransjen.
En annen utfordring ved injeksjonsformning er problemet med leveringstider og fleksibilitet. Når en form er laget, kan det være vanskelig og tidskrevende å endre produksjonsplaner eller design. Å lage en form kan ta fra 5 til 10 uker, noe som gjør det utrolig vanskelig å tilpasse seg plutselige markedsendringer eller designendringer. Denne stivheten krever ofte nøyaktig forplanlegging og investering for å sikre at alt stemmer overens med produksjonsmålene.
Populære Injeksjonsformningsprodukter
Injeksjonsformning gjør det mulig å produsere en rekke av nødvendige komponenter for ulike anvendelser. Et merkbart produkt er TPE Moll Plast Gummistopp designet spesifikt for bilknapper. Denne komponenten er laget for å møte strikte krav til både ytre diameter og hårdehet, for å sikre konsekvent kvalitet og pålitelighet i automobilanvendelser.
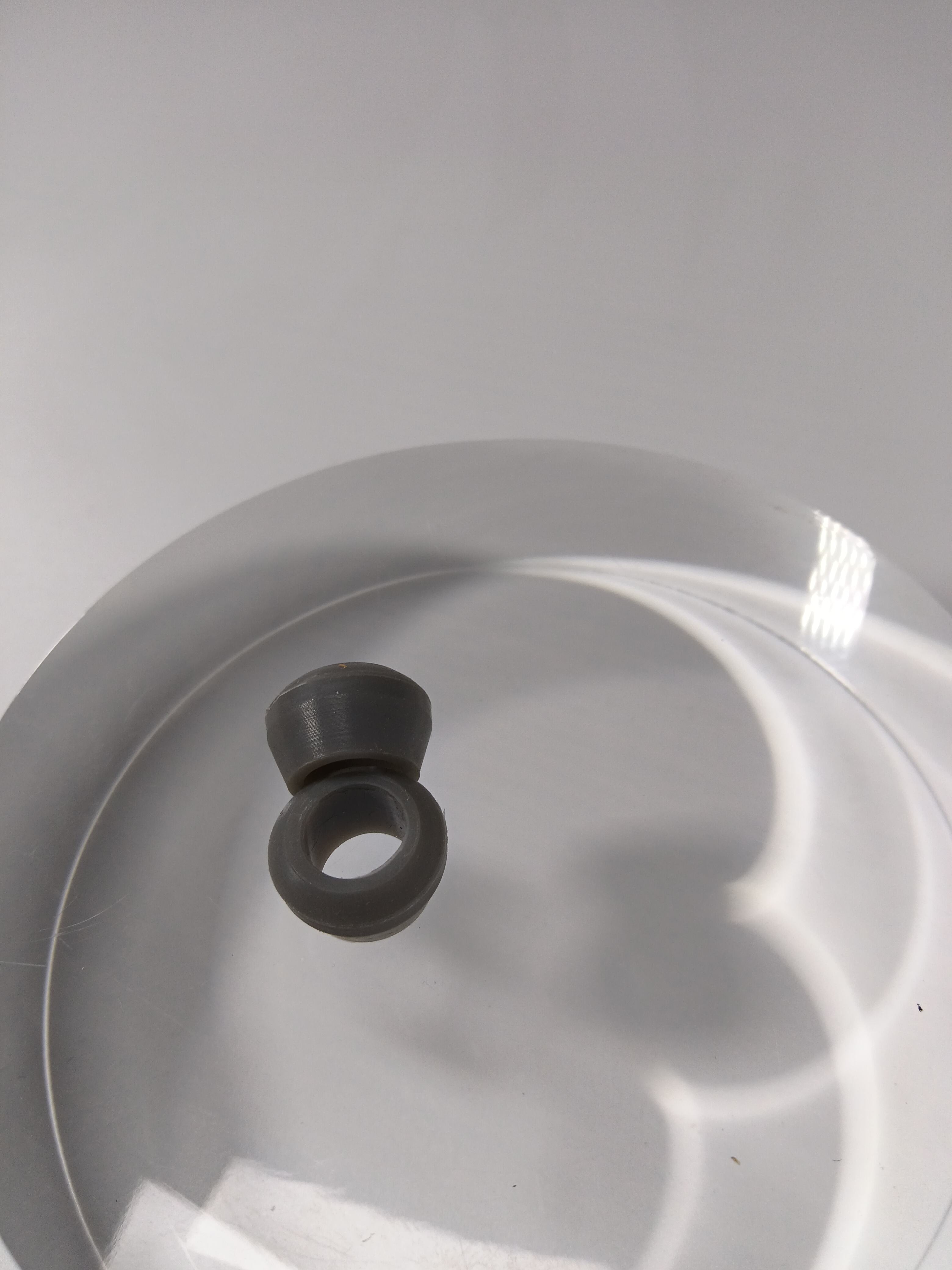
En annen viktig produkt er Det er ikkje tiltrengd eit av dei ulike utgjevningsmateriala. . Dette elementet utnytter de fremragende egenskapene ved Aluminium 6061, som gjør det til en ideell valg for sikkerhetsapplikasjoner. Støttetangen tilbyr høy styrke og varighet, noe som gjør den egnet for bruk i både kommersielle og private alarm-systemer.
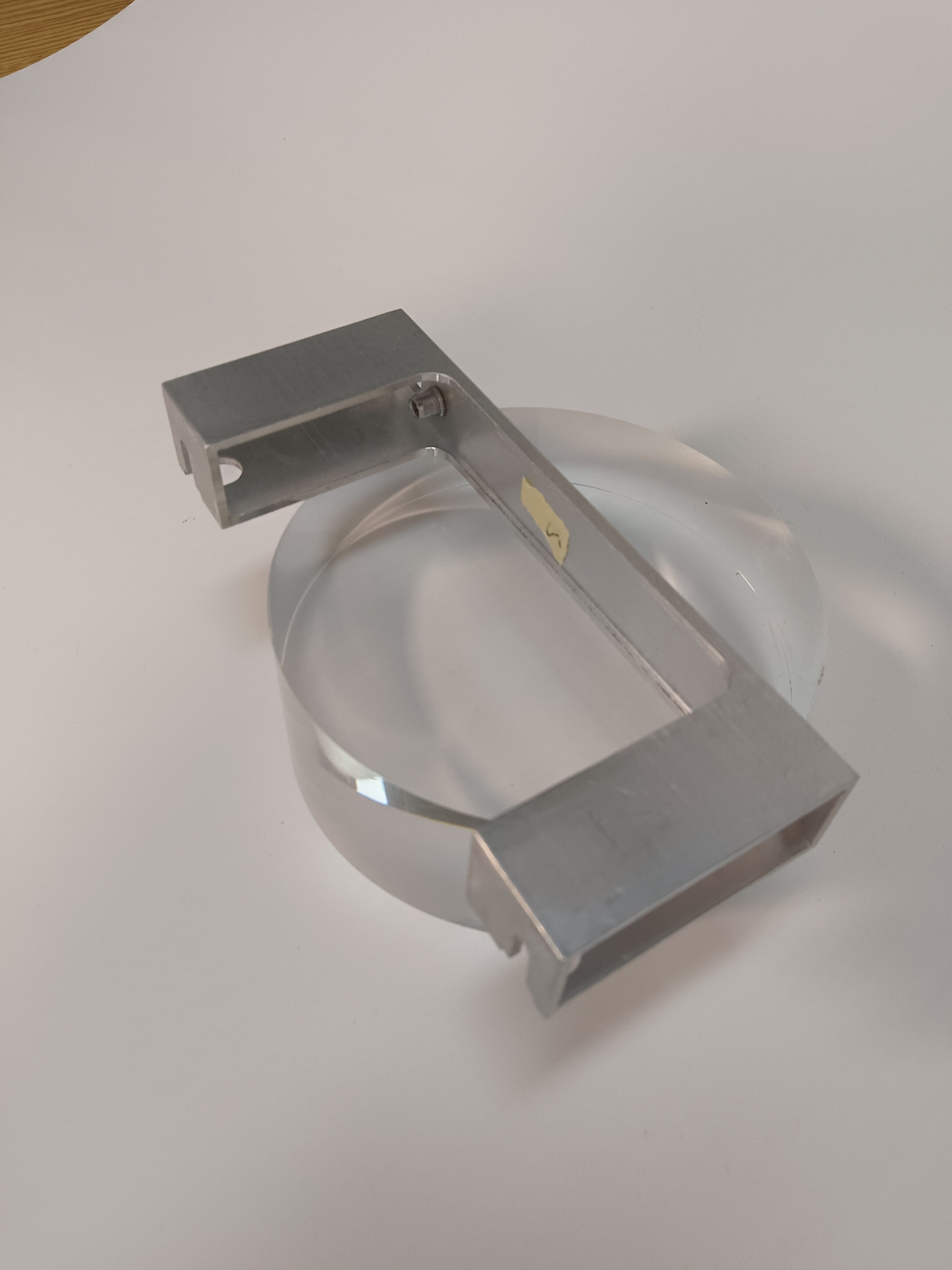
I tillegg, den Gjennomsiktig PC-plastik-sprøytingsbeholder for utstyr for støping er et merkningsverdig produkt som tilbyr ekstraordinær synlighet og styrke. Dette komponentet er spesielt nyttig i applikasjoner som krever klar observasjon av støtteholderen, som i motorensUtstyr, og er designet for å gå igjennom strenge kvalitetskontroller for å sikre pålitelighet.
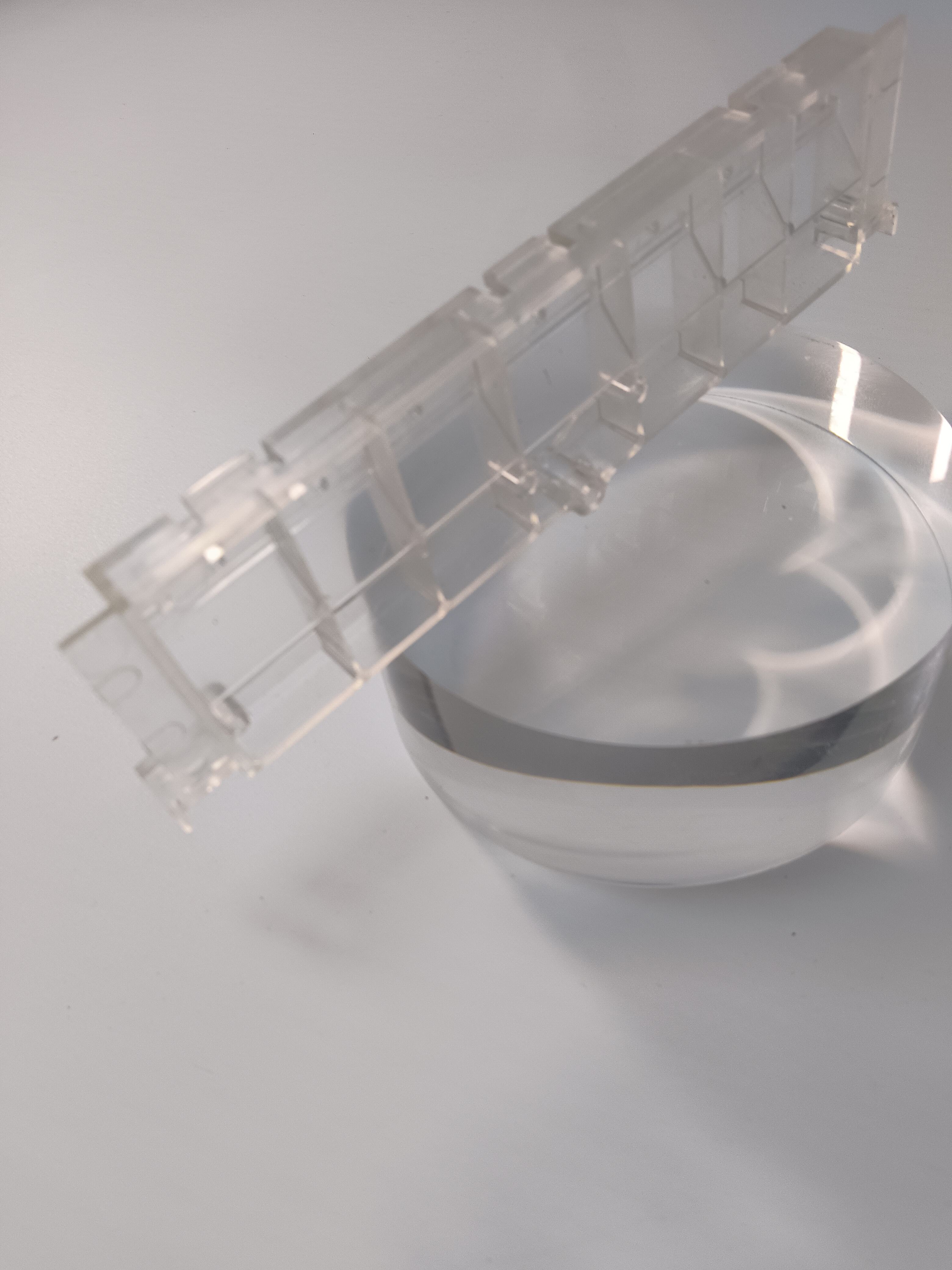
Disse produktene illustrerer de mangfoldige anvendelsesområdene og fordelsene ved injeksjonsforming ved produksjon av spesialkomponenter for ulike industrier.
Fremtidige trender innen injeksjonsforming
Fremtiden for injeksjonsforming formes av betydelige fremgangsmål innen materialer, teknologi og bærekraftige praksiser. En av de mest lovende utviklingene er oppkomsten av bio-baserte plastikker. Nylig forskning understryker deres potensiale til å redusere miljøpåvirkningen beträchtlig samtidig som de opprettholder egenskapene som kreves for høy ytelse. Bio-baserte materialer kan transformere industrier ved å tilby et bærekraftig alternativ til tradisjonelle petroleum-baserte plastikker uten å kompromittere kvalitet eller pålitelighet.
Teknologiske innovasjoner omformer også injeksjonsmoldingsprosesser. Integrasjonen av 3D-skriveteknologi med tradisjonell injeksjonsmolding er en merkverdig trend. Denne hybridløsningen tillater rask prototyping og tilpasning før masseproduksjon, noe som forbedrer effektiviteten og reduserer leveringstidene. Ledende selskaper som Stratasys og DDM har allerede begynt å implementere disse teknologiene, banende vei for en ny era av fleksibel produksjon. Dessuten har framsteg innen automatisering optimert produksjonen, minimerende feil og reduserende kostnader.
Bærekraftighet er et avgjørende fokusområde i injeksjonsmoldingsindustrien. Selskaper adopterer stadig mer gjenbruksløsninger, som bidrar til å redusere avfall og bevare ressurser. I tillegg blir energieffektive prosesser standardpraksis, drevet av industrens engagement for å redusere karbonfotavtrykket. Som fremhevet i nylige bransjetrender, støtter disse praksisene ikke bare miljømål, men forbedrer også driftseffektivitet og kostnads-effektivitet, noe som lar produsenter møte økende markedsevner på en bærekraftig måte.
Konklusjon: Framtiden for Injeksjonsmolding
I konklusjon, er injeksjonsmolding fortsatt et sentralt element i produksjonen, kjennetegnet ved effektivitet og tilpasningsdyktighet. Disse egenskapene understreker dens avgjørende rolle i å forme fremtidige fremgangsmåter innen produksjon. Som bransjen fortsetter å utvikle seg, er potensialet for vekst og innovasjon innen injeksjonsmolding betydelig, med lov om å fortsette å ha innflytelse på ulike sektorer.